LES CLES DU DIMENSIONNEMENT
Ouvrages en commandePhotovoltaïque autonome
Photovoltaïque raccordé au réseau
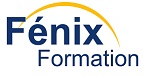
Formations Professionnelles Photovoltaïques
Couche de passivation ou couche passive des inox
La fabrication d’un métal ou d’un alliage s’accompagne toujours de la formation spontanée d’un oxyde en surface du produit, au contact de l’eau ou de l’air humide. Ainsi le fer et l’acier forment de la rouille, l’aluminium de l’alumine, le cuivre du vert de gris.
Les inox produisent en surface un oxyde très fin, composé d’oxydes et d’hydroxydes de chrome de quelques Angströms d’épaisseur. Cet oxyde, couramment appelé couche passive, protège l’inox des agressions extérieures, et lui confère cette propriété appelée l’inoxydabilité, garante de la résistance à la corrosion de ces alliages. La couche passive fait intrinsèquement partie du matériau – contrairement au zinc déposé par galvanisation sur les aciers – ce qui explique que l’inox présente des avantages essentiels.
La stabilité
Une fois formée, cette couche est parfaitement stable puisque son épaisseur reste constante.
L’imperméabilité
La couche passive bloque quasiment tout échange entre le métal et l’extérieur : en cas d’incident sur le matériau (éraflure, découpe, choc, perçage, déformation, etc.), elle se reforme spontanément. Cette autorestructuration est aussi appelée « repassivation ». Les inox sont neutres vis-à-vis de l’environnement.
L’inertie
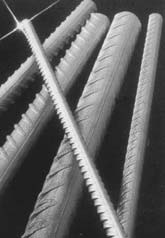
Cependant dans certaines conditions, certains éléments tels les chlorures déstabilisent localement la couche passive, suivant :
- leur concentration ;
- la température du milieu ;
- la nuance de l’inox.